Well Manager Blog
Five Costly Well-System Mistakes Homeowners Should Avoid (and Why DIY Isn’t Always Enough)
When your home relies on a private well, maintaining strong water pressure isn’t just a convenience—it’s essential for daily living. Imagine waking up expecting a
What is Causing My Well Water Issues: Do I Have a Low-Yield Well?
When you rely on a private well for water, daily tasks often come with subtle anxieties. It could be the hesitation before starting the dishwasher,
Is Your “Cost-Effective” Well Pressure Booster Solution Actually Saving You Money?
When you rely on a private well, daily struggles with low water pressure can quickly turn small tasks into major headaches. A weak shower stream,
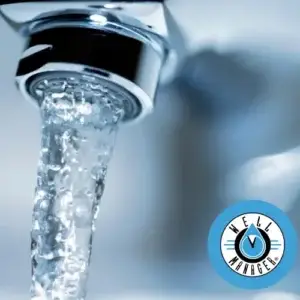
What is the Best Water Pressure Booster for a Low-Yield Well?
You’re probably familiar with the frustration of stepping into your shower, turning on the faucet, and feeling little more than a trickle of water.
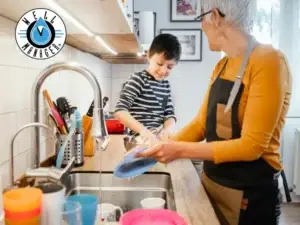
Living Comfortably With a Low Water Pressure Well: How to Boost Your Flow Permanently
It’s frustrating to enter the shower expecting a refreshing burst of water, only to be greeted by a weak, inconsistent trickle. You’re not alone if
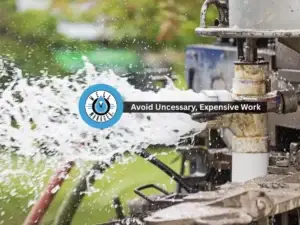
How Do You Permanently Fix Low Water Pressure Well Without Drilling a New One?
Are You Tired of Living with a Low Water Pressure Well? If you’ve lived with a low-yield well, you’re intimately familiar with the daily frustration.
Signs of a Low Water Pressure Well: How To Tell If You Have a Low-Yield Well
Some families notice that routine tasks like showering and running the washing machine simultaneously lead to a sudden loss of water flow. Others experience faucets
Low Water Pressure Well: How Much Water Should a Healthy Well Recover in One Hour?
Many well owners notice pressure dips whenever family routines overlap, like running laundry and taking showers at the same time. It’s natural to wonder if
Does Tank Size Matter for Consistent Well Pressure?
Some households experience unpleasant surprises whenever a faucet is turned on during peak demand. The pressure might initially blast, then instantly dwindle into a weak
Worried About Drilling a New Well?
It’s easy to panic the first time your faucet trickles instead of gushes, especially if your well pump has been around for decades. Many homeowners
Why Heavy Spring Rain Doesn’t Always Fix a Low Water Pressure Well?
It’s springtime, and your region just got drenched with record-breaking rains—yet your well water pressure remains stubbornly weak. Many homeowners assume abundant rainfall is a
Ever Wonder Why Groundwater Deserves Its Own Week?
Imagine turning on your faucet one morning and finding nothing but a dribble. That scenario is more than an idle worry for many Americans—groundwater keeps